Our Products are Designed
to Fit Your Needs
At Pycube, we strive to revolutionize healthcare operations with cutting-edge technology designed to streamline workflows and provide your team with unmatched asset lifecycle and specimen journey visibility. Our innovative solutions empower healthcare providers by offering real-time tracking, advanced digital tools enhanced by AI, and seamless integrations that support both clinical and administrative operations.
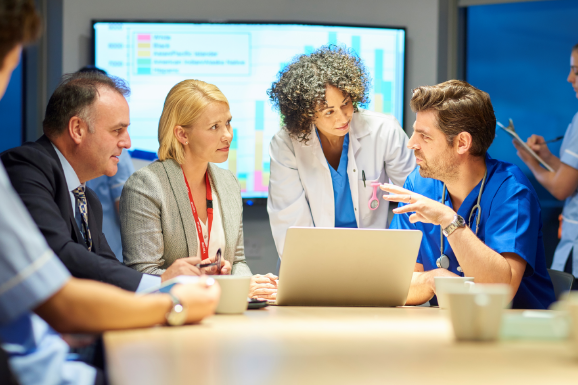
Share an efficiency challenge you are currently facing, and we can build a solution through our platform across any department or multiple departments.
The Pycube Promise
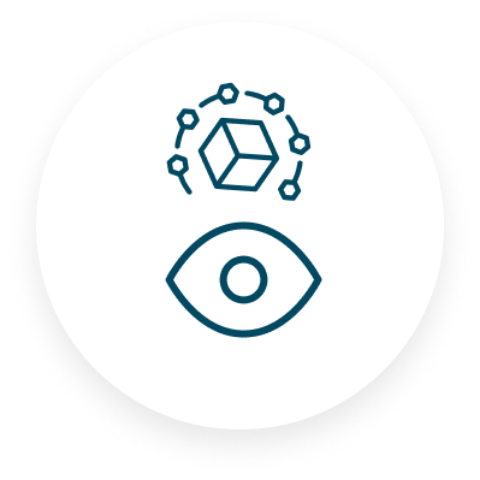
Increased Asset Visibility
Using Passive RFID technology, our solutions give you complete oversight of your medical equipment and specimens. They ensure every asset is accounted for, from collection to use, while providing accountability across the entire asset lifecycle or specimen journey.
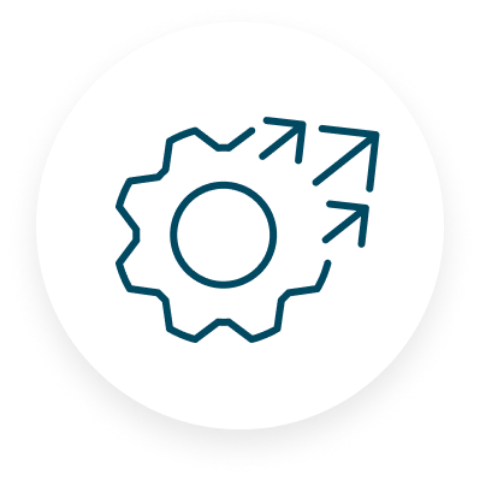
Real-Time Data and Insights
With our cloud-based platform, healthcare teams have access to easily understandable, actionable insights provided by the Pycube Software dashboards. These insights support better decision-making, prevent resource shortages, and improve asset management.
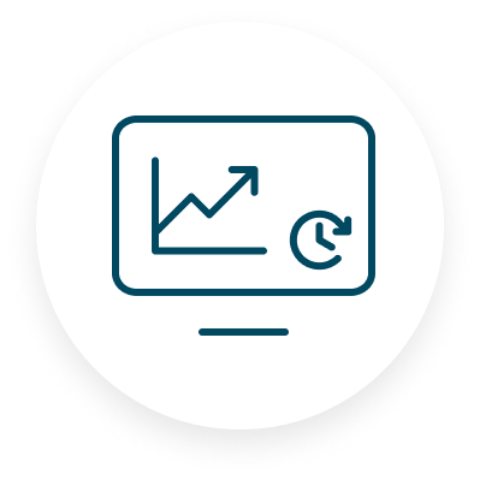
Efficient Operations
By digitally transforming and automating your workflows and asset tracking through Passive RFID technology, real-time AI-enhanced tools provide data insights, and seamless integrations with existing systems, Pycube reduces manual processes and enhances the speed and accuracy of operations.
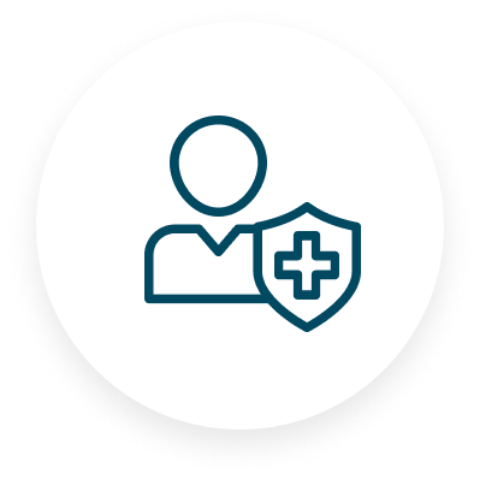
Patient Ready
This leads to lower costs, reduced human error, and more time for your team to focus on what matters most: Patient Care.
Key Benefits
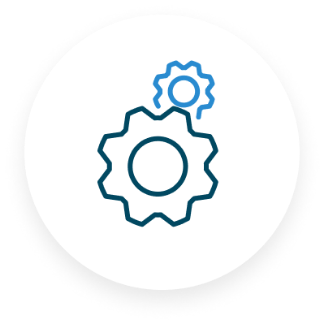
Seamless Integration
Tags are more cost-effective and range in size but are significantly smaller compared to active RFID tags. They come in a variety of sizes and materials to fit the specific needs of each asset being tagged.
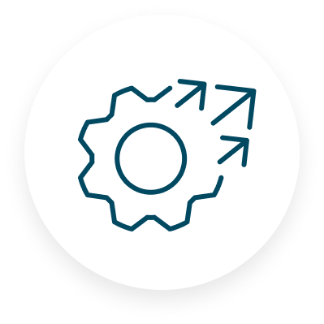
Advanced Process Automation
Our AI-powered tools automate routine tasks, such as documentation, training, manual logs, and more, reducing the burden on your staff and helping them manage resources more effectively.
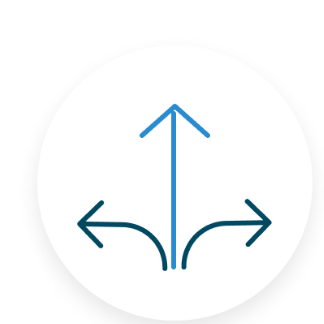
Scalable and Flexible
Whether you manage a small clinic or a large hospital system, Pycube’s solutions grow with your organization, adapting to your unique needs over time.
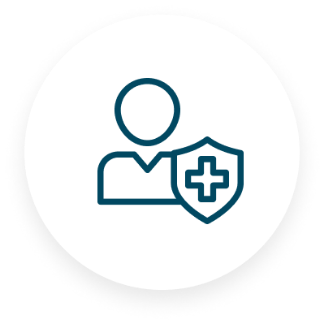
Enhanced Patient Safety
With precise tracking of medical equipment and specimens, we help reduce the risk of misplaced resources, ultimately improving the quality and reliability of care.
Pycube’s next-generation solutions harness smart (or innovative) technology like RFID and AI to transform healthcare operations. By automating asset tracking, specimen management, and routine administrative tasks, our scalable solutions provide real-time visibility, reduce human error, and streamline workflows, enabling healthcare providers to deliver efficient and uninterrupted patient care.
Digital Asset
Medical Equipment Lifecycle
Pycube’s Digital Asset solution directly addresses the critical challenges hospitals face in managing and tracking their medical equipment. Through the use of scalable, battery-less RFID technology and dynamic dashboards, this solution enables healthcare providers to locate, control, and protect their assets in real-time. By automating asset tracking and offering live visibility, the Digital Asset solution significantly reduces operational costs, prevents loss, and ensures that critical equipment is available when needed. This streamlined process helps maintain uninterrupted patient care and optimizes resource management, resulting in more efficient, cost-effective hospital operations.
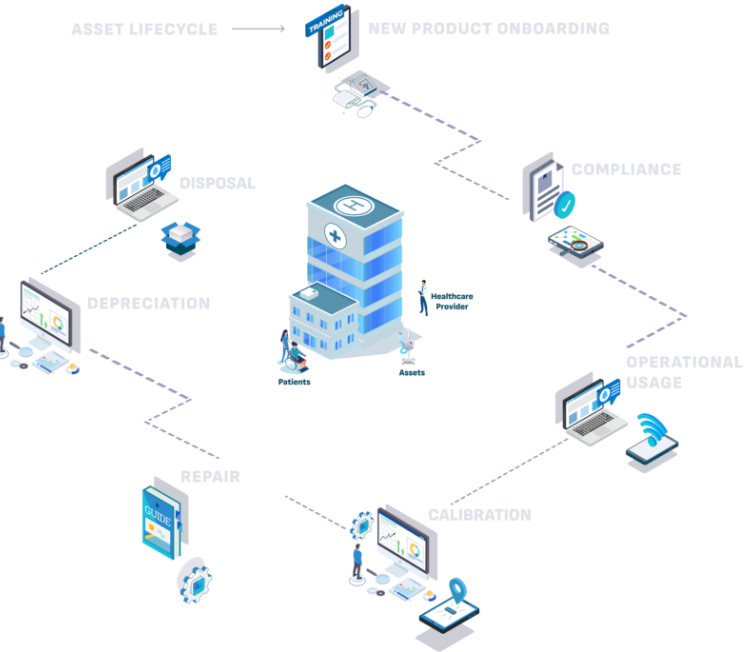
Unlocking Value: Top Use Cases for Digital Asset
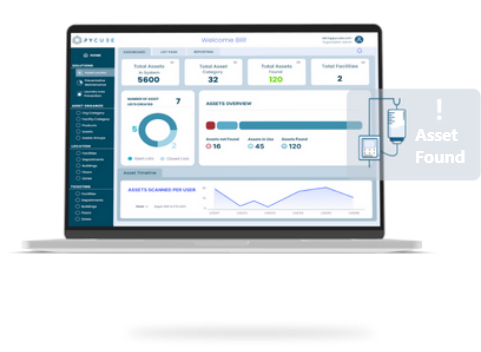
“With The Unparalleled Ability To Look Beyond What Your Eyes Can See, Your Assets Can’t Hide From Pycube.”

Asset Location
With Pycube’s Asset Location solution, finding specific assets has never been easier. Pycube’s dynamic software, combined with mobile passive RFID technology, lets you conduct targeted searches from asset lists that you create to detect specified assets from dozens of feet away without the need for an obstruction-free line of sight. With the unparalleled ability to look beyond what your eyes can see, your assets can’t hide from Pycube.
Benefits
Dynamic software with mobile passive RFID.
Targeted searches from asset lists that you create.
Locate assets from a dynamically adjustable distance without the need for obstruction-free line-of-sight.
Live dashboard makes location information available
on demand.
Integrate one of our AI tools to reduce manual work and staff burnout.
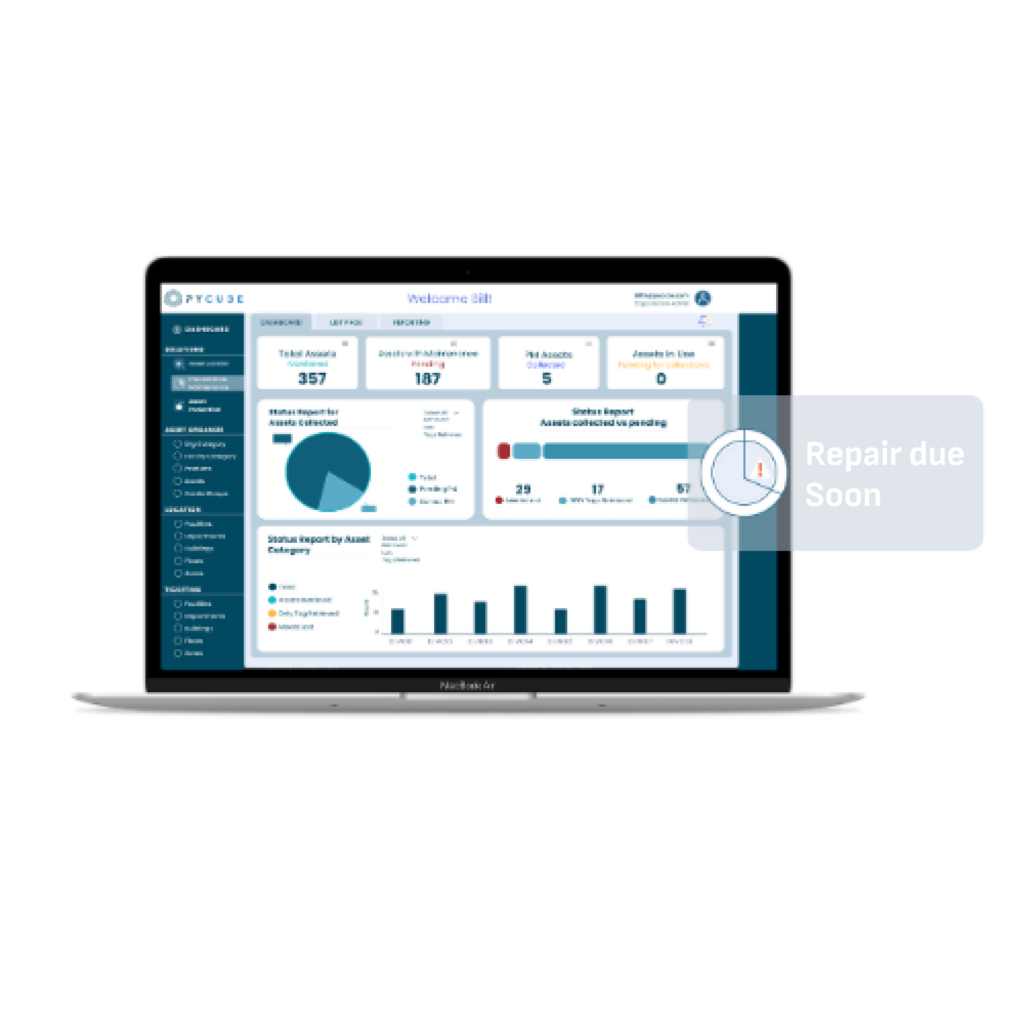

Preventative Measures
With Pycube’s PM, save time and worry with automatically generated lists of assets due for preventative maintenance. Pycube’s live dashboard makes real-time information about your tagged assets’ last known locations and movement available on demand so you can quickly locate assets for PM. The software also allows you to track progress on asset collection and update maintenance schedules. Stop searching for the needle in the haystack – eliminate the haystack with Pycube.
Benefits
Live dashboard provides real-time information about your tagged assets’ last known locations available on demand to quickly locate for PM.
Conduct targeted searches to locate a specific device among a mixed group.
Software allows you to track progress on asset collection and update maintenance schedules.
Integrate one of our AI tools to reduce manual work and
staff burnout.
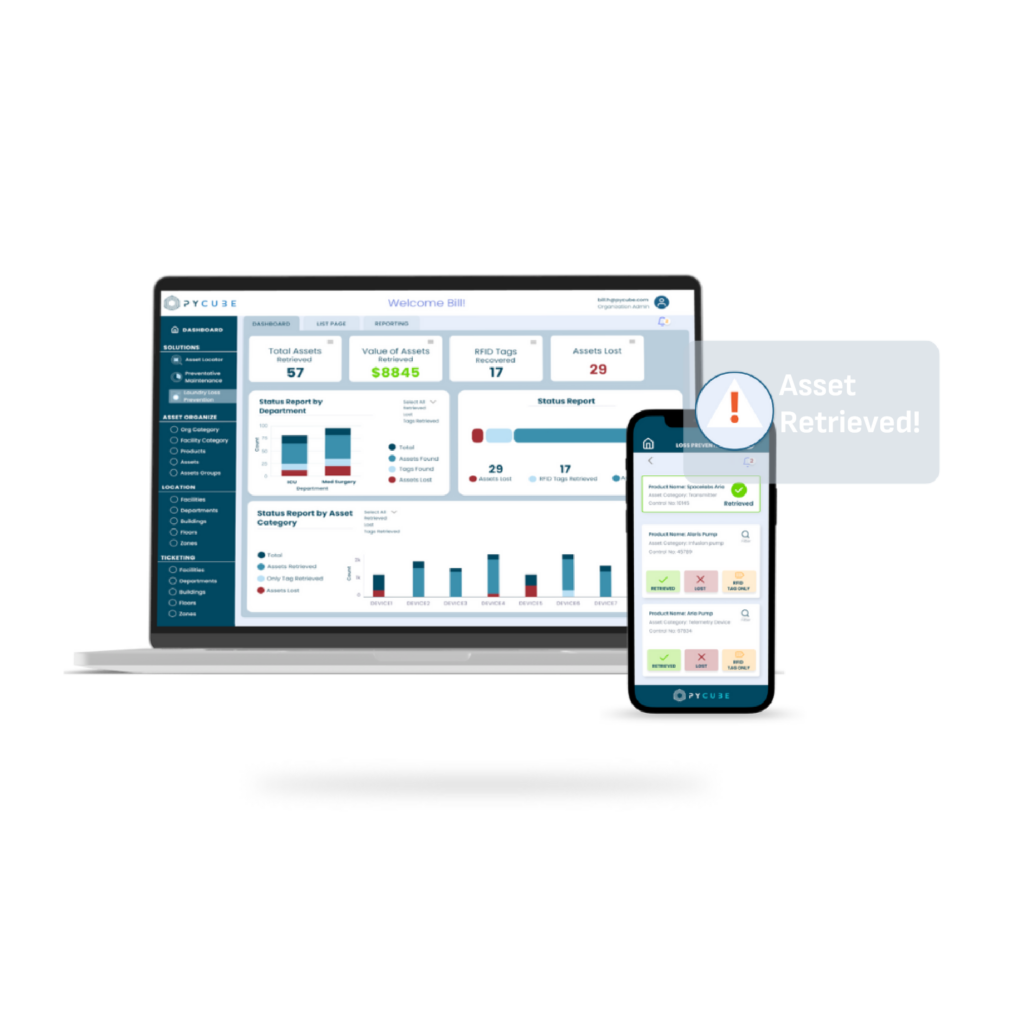

Asset Protection
Pycube’s Asset Protection solution combines passive-RFID technology with Pycube’s business intelligence software to quietly monitor your assets’ locations and movement and proactively notify you of unauthorized asset movements, such as through RFID gates at facility exits or laundry rooms. Catch run-away assets before they’re gone for good with Pycube.
Benefits
Quietly monitors your assets’ locations and movement.



Digital Specimen
Clinical Specimen Journey
Pycube’s Digital Specimen Solution offers a comprehensive approach to managing and tracking clinical specimens, ensuring complete visibility and accountability from collection to final analysis. By leveraging RFID technology and AI-enhanced analytics, our solution automates the entire specimen tracking process, reducing human error and preventing specimen loss. This solution seamlessly integrates with existing workflows, empowering healthcare providers to streamline operations, enhance patient safety, and improve efficiency through real-time data analytics.
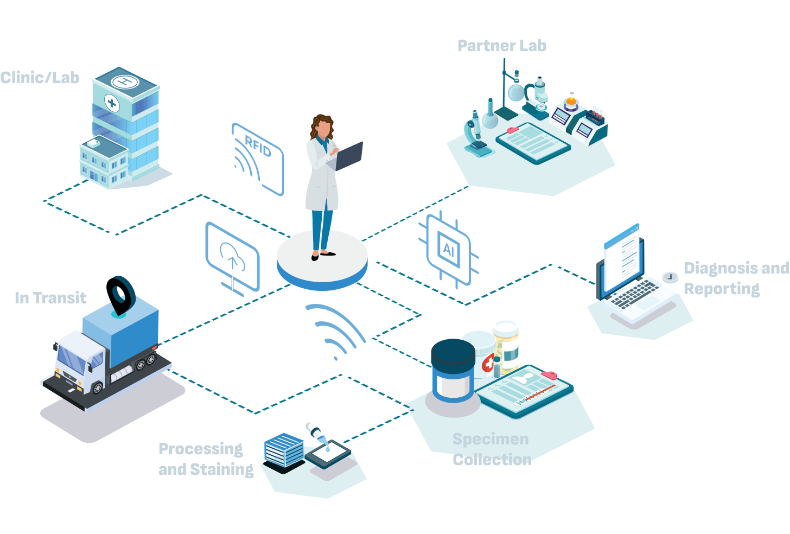
Current Challenges
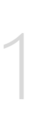
Lack of visibility into specimens
collected, before they reach
the lab
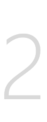
Lack of visibility into specimen
handling from collection to
delivery
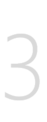
Lack of visibility into specimens
collected, before they reach
the lab
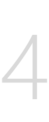
Lost specimens are detected
too late
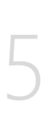
Specimens may be misplaced
or lost due to too many touch
points
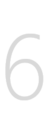
Multiple specimens are shipped
together in a single box, then
unboxed and sorted later, making
tracking challenging
Digital Specimen Tracking Solution
Specimen tracking notifications at every touch point!
Essential Features & Benefits of Digital Specimen
By implementing advanced tracking systems, hospitals can

Prevent Specimen Loss
Proactive Notifications and alerts of missing specimens – reducing patient, regulatory, and legal risk
Enhance Patient Safety
Digital specimen collection and workflow – next-gen technology that prevents the loss of specimens and improves patient safety
Automate and Integrate into your current Workflow
AI-enabled data analytics – enabling quality initiatives, training, and compliance
Improve Efficiency with Data Analytics
IoT for clinical specimens – ensuring the right patient gets the right diagnosis at the right time
Digital Supply Chain
Real-Time Visibility
In today’s healthcare environment, the efficiency and reliability of the supply chain are critical to both patient outcomes and operational success. Hospitals and health systems face increasing pressure to manage resources more effectively, reduce costs, and ensure compliance with stringent regulatory standards—all while adapting to rapidly changing clinical demands.
Pycube’s platform offers scalable, modular solutions designed for healthcare’s unique operational challenges. Our system integrates seamlessly with existing infrastructure, minimizes work flow disruption during implementation, and deilvers immediate, measurable impact.
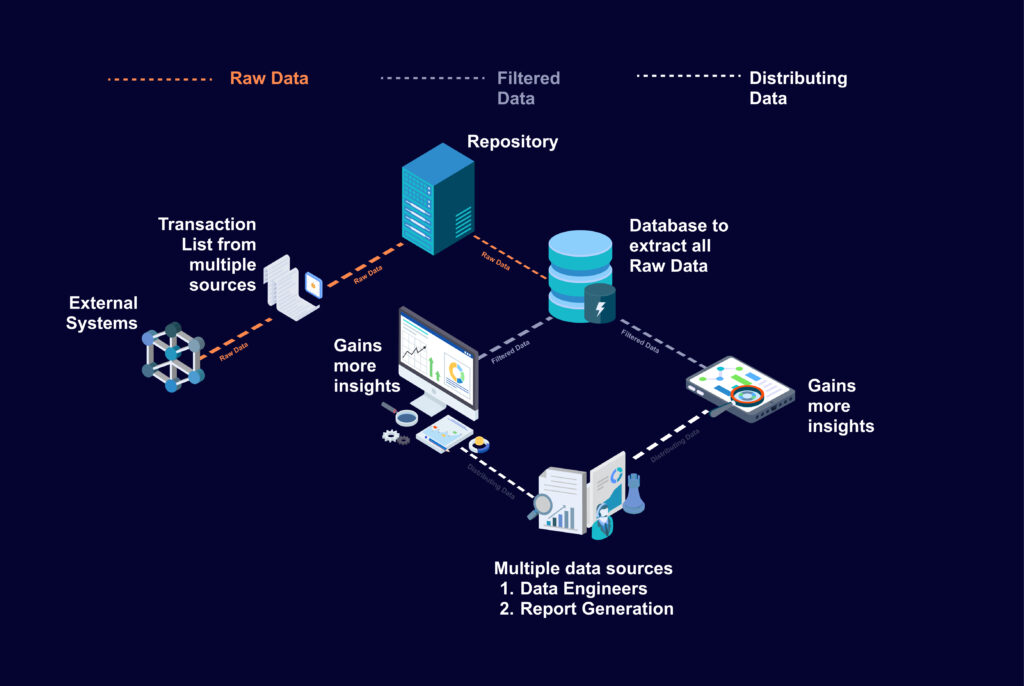
Smarter Invoice Automation & Vendor Oversight
Auto-Standardized Invoices
Seamless Vendor Integration
Built-In Fraud Detection
Help your team increase productivity.
Customer Stories
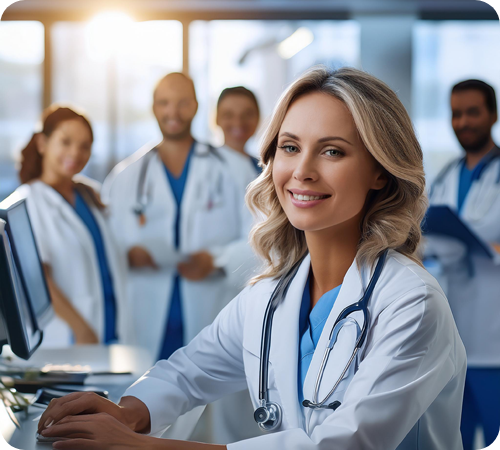
An extensive hospital system in Texas is needed to streamline asset management across multiple facilities, implementing complete visibility of asset locations and preventative maintenance workflows. With Pycube’s hands-on support, they gained confidence in managing thousands of assets independently within a month. While the tagging process for over 88,000 assets continues, our customized workflows ensure efficient asset tracking and maintenance, empowering the hospital system to prioritize patient care.With Pycube’s Asset Location solution, finding specific assets has never been easier. Pycube’s dynamic software, combined with mobile passive RFID technology, lets you conduct targeted searches from asset lists that you create to detect specified assets from dozens of feet away without the need for an obstruction-free line of sight. With the unparalleled ability to look beyond what your eyes can see, your assets can’t hide from Pycube.
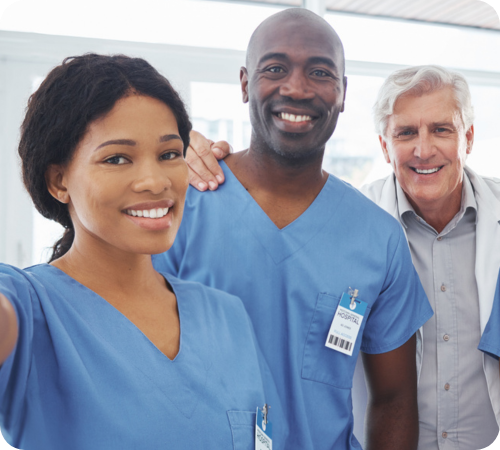
A major New York hospital was having difficulty keeping track of their assets and keeping them from leaving the facility. Pycube used asset loss prevention solution to alert the hospital using real-time notifications and audible alarms to alert when assets pass through a designated choke point, allowing staff to react accordingly and save assets from leaving the facility.
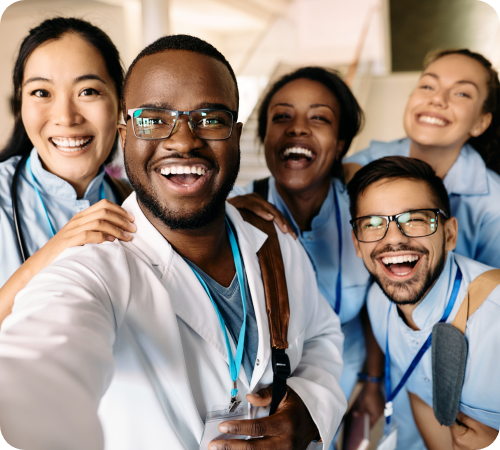
A critical aspect of an emergency department is ensuring that staff and equipment are available and ready to go at all times. Optimizing equipment availability is an essential part of patient management, especially when dealing with a high number of emergency and trauma cases. Pycube’s asset management solution helped this hospital ensure the availability of its assets with improved staff efficiency throughout the patient care cycle, starting from when the patient is admitted to when they’re discharged.